Walker Filtration Inc. Warehouse Expansion Plan with David Donahue, Operations Manager
The decision between moving up or moving out as the investment in the Erie, Pennsylvania office continues
Posted on September 9th, 2021
David Donahue is the Operations Manager and member of the Senior Management team at Walker Filtration Inc., the American Division of Walker Filtration. David is responsible for overseeing the materials, production and quality team. David has been with the company for over eight years and focuses on executing the operational logistics to support the company’s growth and customers.
Written by: David Donahue
Walker Filtration has experienced substantial growth over the last few years and has plans to introduce many new products in the coming years. As our office continues to onboard more customers and prepares to stock new products, we are left with the fortunate task of making room for growth.
Earlier this year, we reached a point where we had maxed out the storage capacity under our current layout. As a result, it was evident we needed to develop a plan that would help add value to the business today and support our future growth.
Our team quickly determined the project’s four main goals that needed to remain at the center of our expansion plans. The four central pillars were to:
- increase storage capacity
- improve efficiency
- improve safety
- minimize business disruption
The Process: Move Out or Move Up?
In 2019, Walker Filtration identified several opportunities within new markets and researched and developed new products to meet the needs of those customers. As the Operations Manager, it was my job to ensure we would have staff available, facilities for storing materials and the appropriate processes in place to support these new products and markets. For several months I worked with a team for input, and we contacted engineers and consultants to help develop a solution that would support all four pillars of the project.
Several solutions were brought to the table. We seriously considered moving facilities, but that would have been costly and disruptive to our business and customers. So, instead of moving facilities, we were trying to find a solution within our current location. Since we have an empty lot next door that could be purchased, we debated expanding our existing footprint. However, that would result in higher ongoing operating costs.
We then considered complex racking and storage structures but again, that did not support our four pillars. There were concerns for employee safety and would have higher prices. This option also required additional staff and added new, complicated work processes.
In the end, the input from the staff on the warehouse floor and analysis of stock volume data aided in finding the best solution.
“Dave, along with the entire operations team, has carefully planned our expansion to maximize space and efficiencies, to allow for significant future expansion while at the same time improve upon our already high expectations of customer service and response times. This is an excellent example of our commitment to our customers and growth in the US market.”
– Richard Taylor, President and General Manager
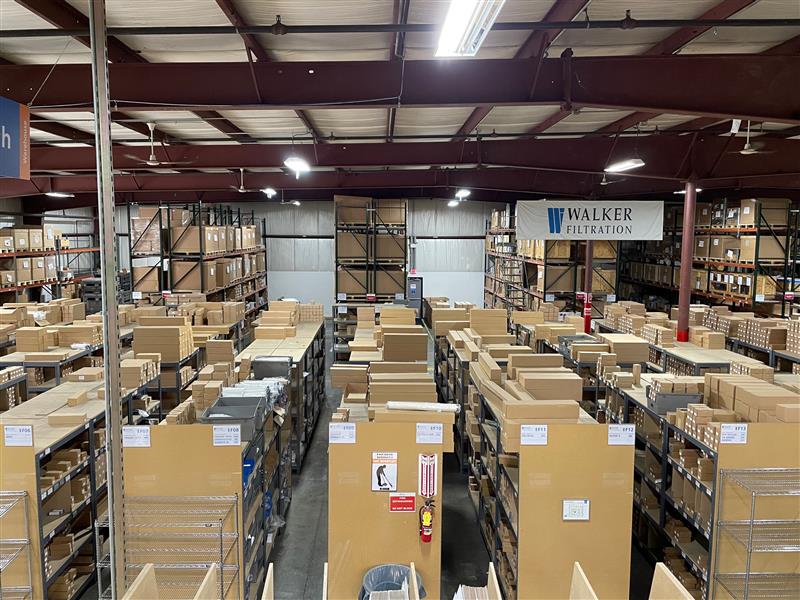
Before Photo of Warehouse Space
The Solution: Moving Up, Not Out
In simple terms, the final solution was to invest in our existing facility by replacing our 23 rows of 7-foot-high racking with 8 rows of 18-foot-high racking.
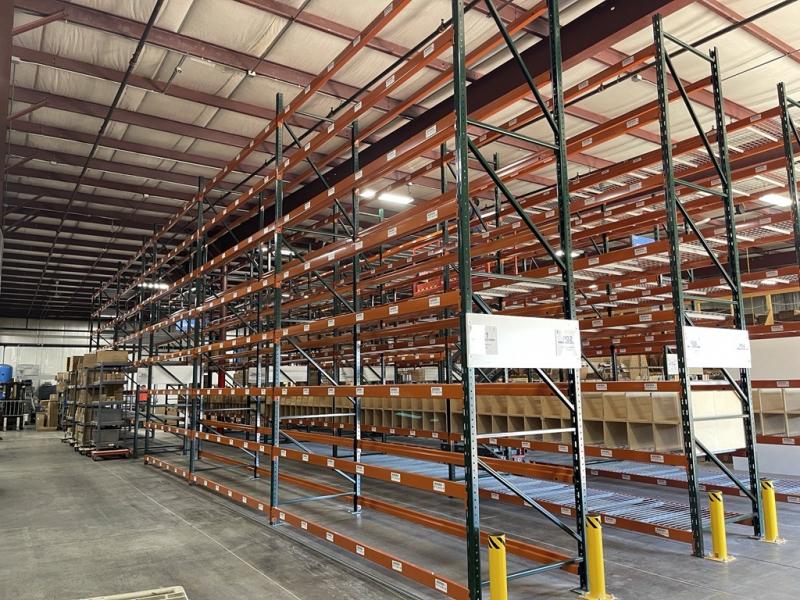
During racking installation
The implementation of the project had many steps, including:
- Relocating product under a temporary storage
- Off-site storage for select products
- Dedicated staff to work additional hours and in different roles
- Additional temporary labor
- Relocation of several thousand parts, both physically and in our ERP system
- All new warehouse signage and bin location labels
- New processes which include barcoded locations
We planned on the transformation taking ten days and Walker Filtration Inc. would remain operational throughout this period to maintain our service to our customers. Like any large-scale project, not all aspects went exactly as planned, but the team was able to overcome any minor issues that occurred and come together to execute this ambitious transformation.
Choosing to Invest in Walker Filtration Inc.
The employees at Walker Filtration Inc. were involved in many steps of this project. From the senior management team to the entry-level staff, their time and energy were essential to our expansion plan’s success. This project would not have happened without them.
We have nearly doubled our previous storage capacity through improved utilization of available shelf space and increased racking height without changing the footprint of the warehouse. The final layout that we chose is modular in design and will allow us to add 25% of handpicking storage and 54% more pallet storage in the future as we continue to grow.
The investment in our current facility in Erie, PA, is a sign of Walker Filtration’s dedication to our current and future staff and the Erie community. We are serious about our growth plans, and with that comes the need for adding new members to an already talented team.
Over the coming year, we anticipate hiring for positions in our warehouse, material control and sales teams. If you are in the Erie area and are looking to join a growing company where you’re not just a number but an impact player, visit our careers page for current open opportunities or reach out to us at usa@walkerfiltration.com.